CNC Tool Finder: By Milling Operation
Choose the milling operation you will be doing on your machining job and see our recommended tools for that purpose. Other tools may also accomplish the job, but these will be the best performing mills for that operation.
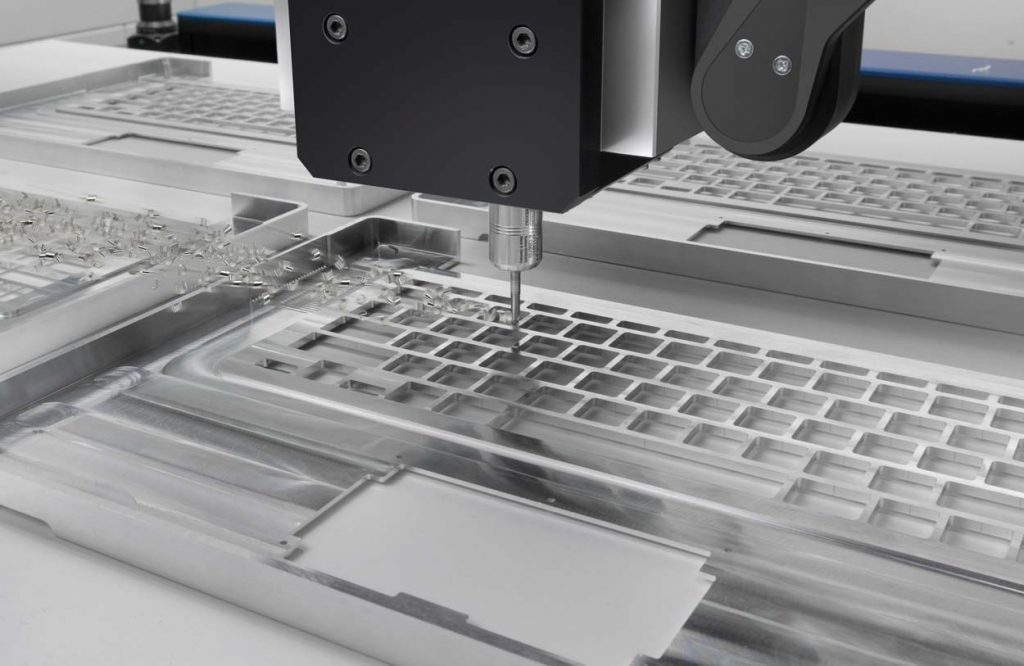
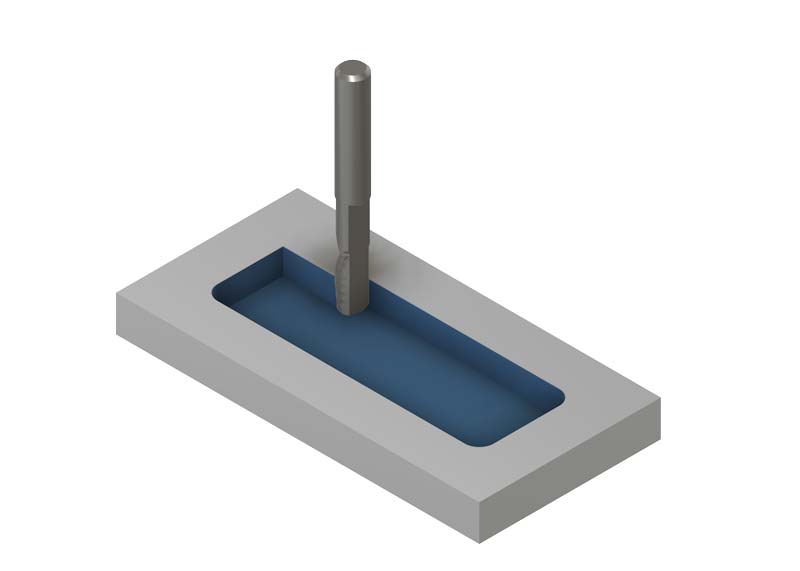
Roughing
Roughing involves removing bulk material rapidly and roughly shaping a workpiece into the desired form. Tools with fast feed rates and large depth of cut are ideal to remove as many chips as possible in the shortest amount of time.
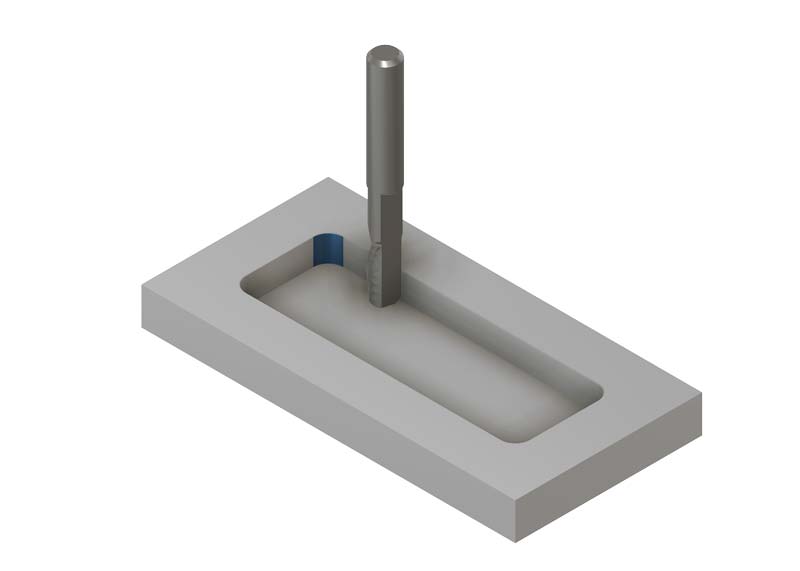
Finishing
Finishing is the final step of machining; its purpose is to enhance the appearance of a part and remove any aesthetic flaws like machining marks. Tools with very sharp and polished cutting edges provide superior surface finishes.
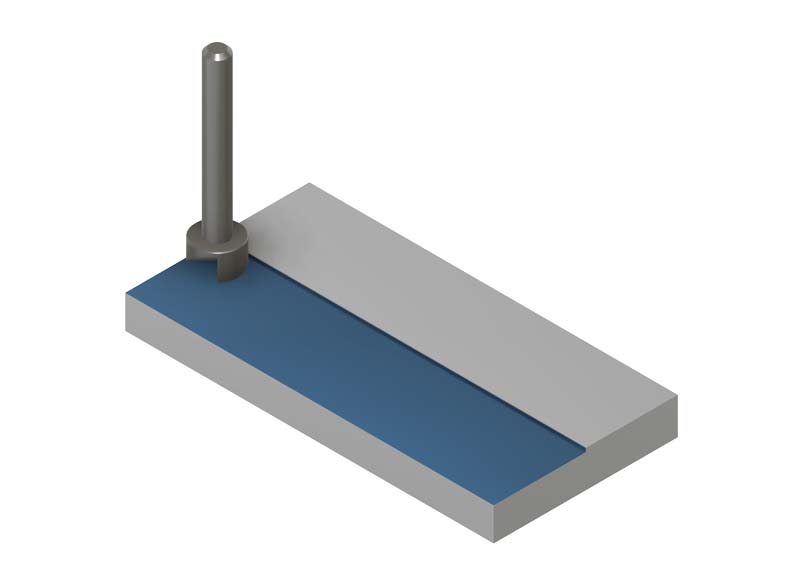
Facing
Facing removes material from a workpiece to create a flat surface. The purpose is to achieve a level surface that is square with the axis of the part. Tools with wide cutting edges are most effective for quickly truing up material.
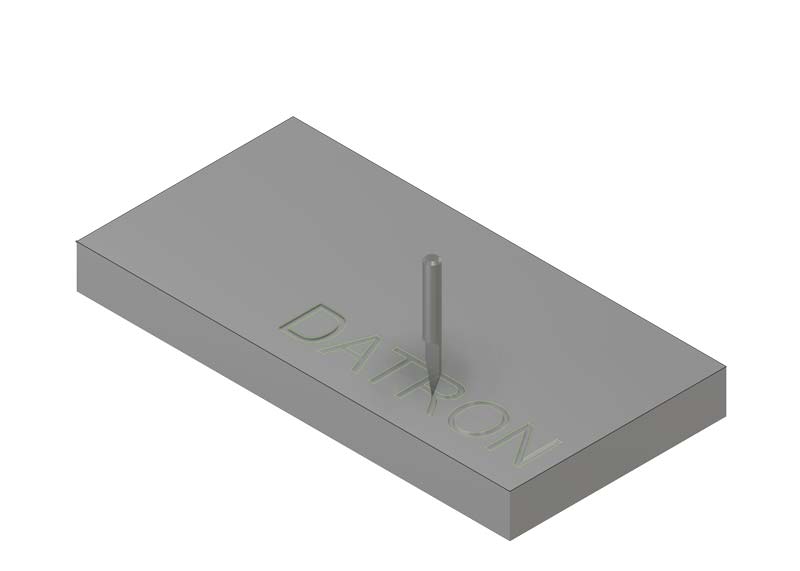
Engraving
Machine engraving is the process of carving a design into a material, often used to decorate or label a part. Small, intricate details are common in engraving applications and require tools that are optimized for high-speed spindles.
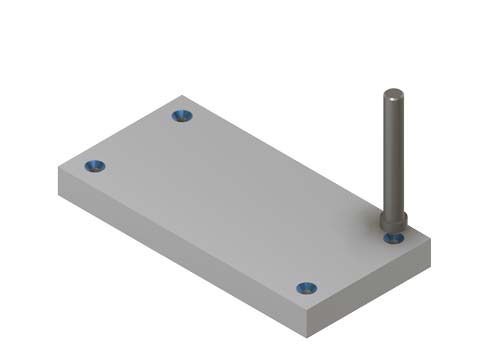
Countersinking / Chamfering
Countersinking is used to widen a drilled or tapped hole, so a screw sits flush or below the surface. Chamfering removes sharp edges by leaving a sloped surface. These tool types can perform several operations like deburring and beveling.
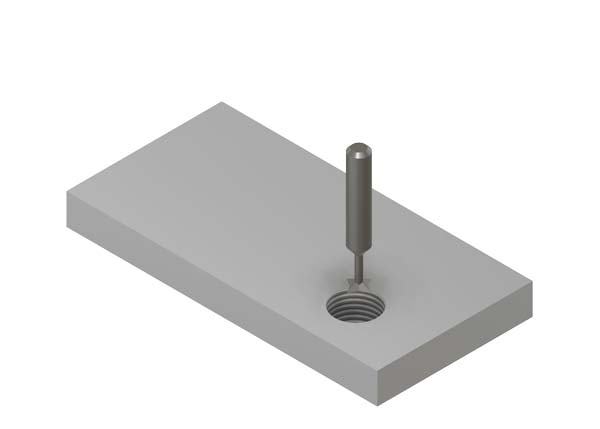
Threading
Threading is the process of cutting screw threads, so parts can be fastened together. Thread mills let you control the fit, adjust the thread size, and create custom threads which keeps run times low since there are fewer tool changes.
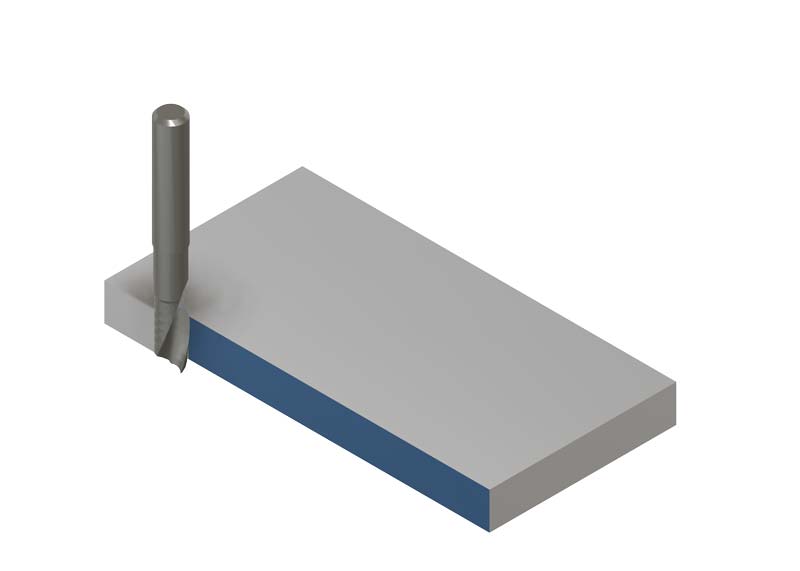
Profiling
Profiling involves roughing or finishing vertical and slanted surfaces, like convex and concave shapes in two or three dimensions. Tools that provide smooth surface finishes and have high material removal rates are best for this operation.
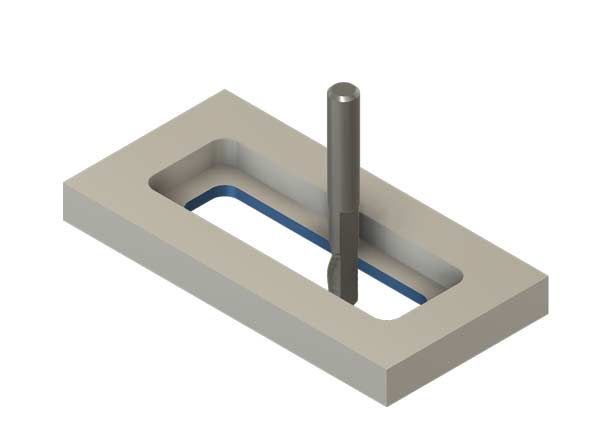
Pocketing/Deep Milling
Pocket milling removes material inside a workpiece to a fixed depth. Long-reach tools are recommended for this operation since the reduced diameter above the cutting edge prevents the tool from scraping against the part wall.
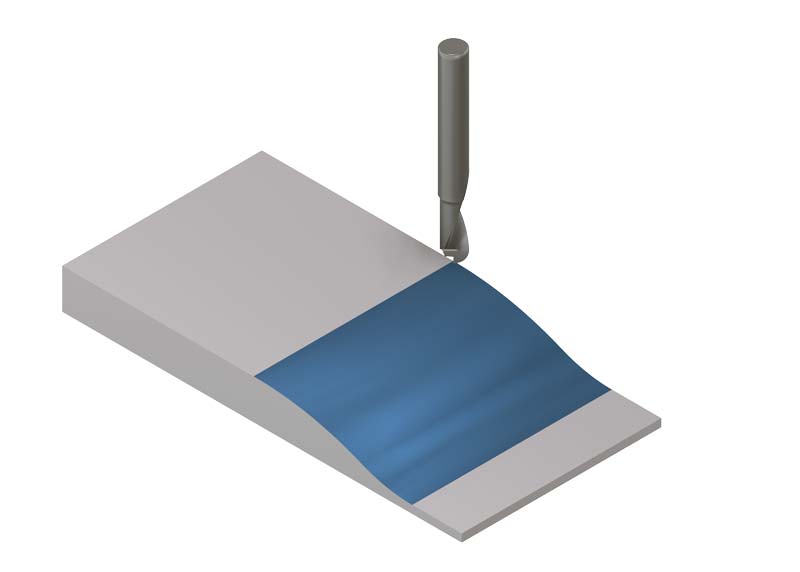
3D Surfacing
3D surfacing is when the X, Y, Z axes are moving at the same time. This operation often has more complex toolpaths that require multiple passes. Ball nose end mills are recommended as the rounded cutting edge cuts material at any angle.
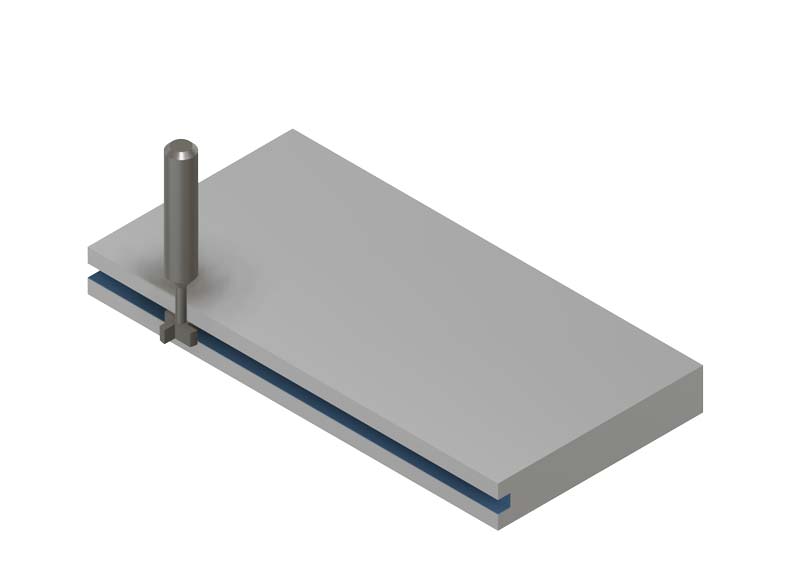
Undercutting/Slotting
Undercutting creates a recessed feature in a part, and that requires special tooling. A standard end mill can’t do it as the area is often inaccessible from overhead. The tools need to be able to bevel or deburr the underside of a part.
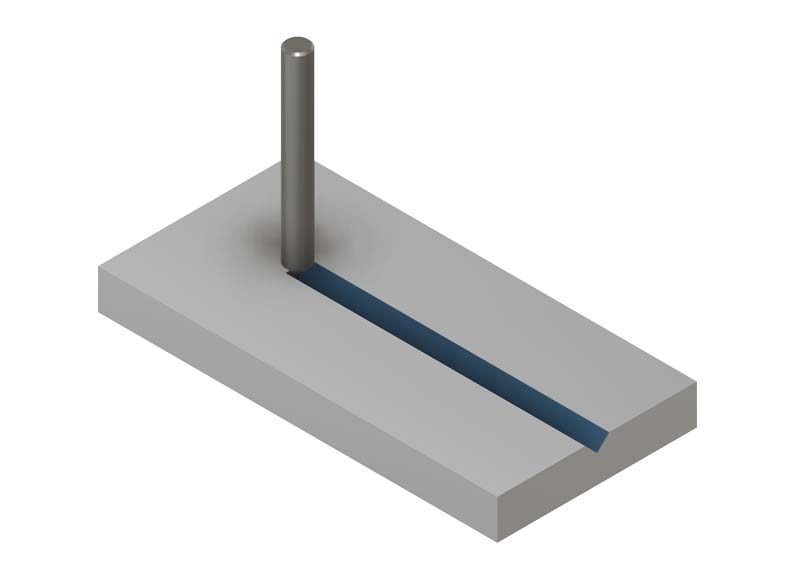
Grooving
Grooving, which is also known as recessing or necking, is the process of creating a long and narrow indentation in a workpiece. This operation needs tools with proper chip evacuation in order to avoid chip buildup and tool breakage.
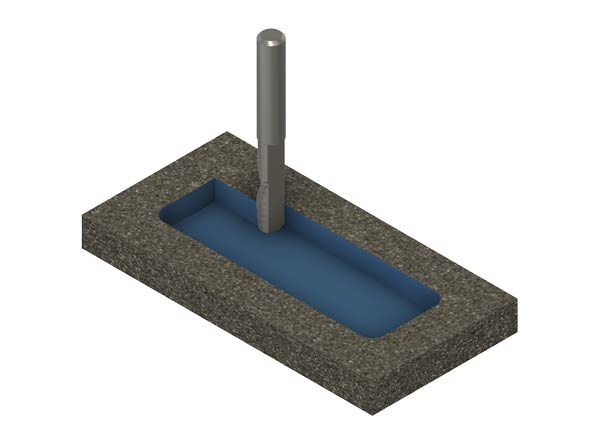
Foam Cutting
Milling foam is difficult as the soft material tends to move or fold away from the cutting force, leaving poor-quality edges. To produce clean edges, you need tools with very sharp cutting edges that are designed for high-speed machining.
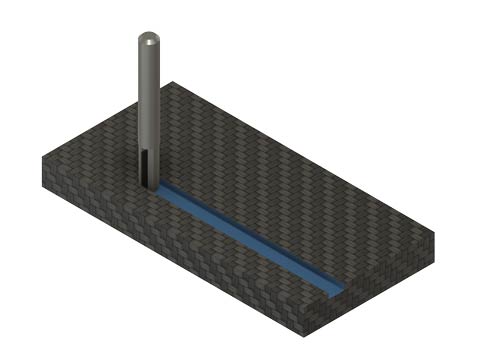
Glass Fiber Composites
Composites are challenging to machine as the material is abrasive and prone to delamination and splintering. Coated tools are recommended since the hard materials wear tools out fast, and the coatings are designed to protect and prolong your tool life.
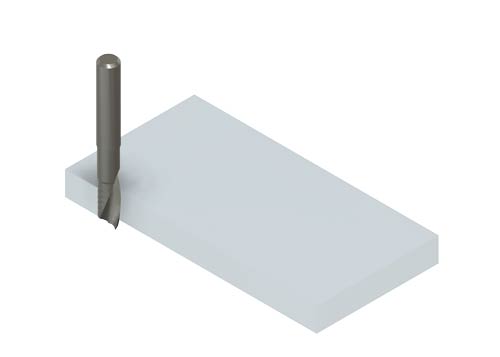
Polished Finishes in Plastic
When machining plastic, if a tool’s cutting edge isn’t sharp enough, it will tear the plastic and create a matte, cloudy finish. Tools with extremely sharp and polished cutting edges are recommended to achieve high-quality finishes.